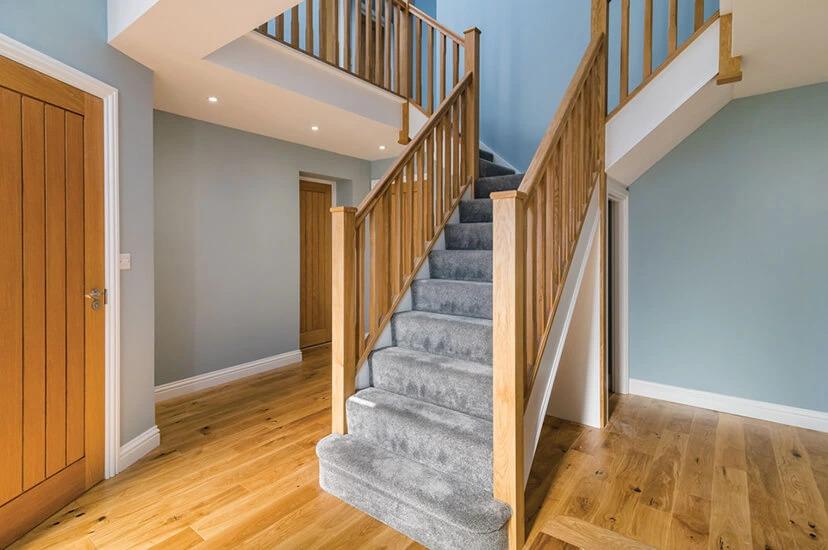
Step Ahead Stairs is a company specialising in the manufacture and installation of residential and commercial stairways. Their concentrated focus means they can deliver a high-quality product at an economical price, more efficiently than general builders who use them a lot.
Ryan Kaden, the business owner, tells us how CNC routing has transformed their prefabrication process.
Looking ahead outside the square
“I came back from mining in Perth a couple of years ago to take over the business from my father, who wanted to scale down his work. I was wondering about technology to improve production efficiency and I heard about CNC routers.
So I looked to Google to see what was out there and found James. It was great that he was local, unlike most of the suppliers who were in Auckland. I didn’t want to have to get them all the way down here to deal with issues.”
The right solution for us
“So I met James and we talked about machine options. He offered a very competitive price compared to others. We went through the investigation process and I ordered a machine.
When it arrived, there was a lot to take in, but James got us through it all. We just had to get ‘time in the seat’ to get the hang of it.”
Faster and Sharper
“Now we can cut out staircase stringers, treads, and risers in 1/4 of the time instead of previously with a template and hand-router. The CNC router cuts it out precisely to fractions of a millimetre, making a better finish for the product.
He’s currently helping with a program to fabricate kite winders, where the staircase turns 90° with three, four, or five steps, like cheese segments.”
Immense support
“James has been amazing – an understatement – doing everything from designing to fixing. Without him, we would have been way behind.
Whenever we need anything, James puts his foot forward to take care of it. He’s extremely helpful and is only 15 minutes away.”